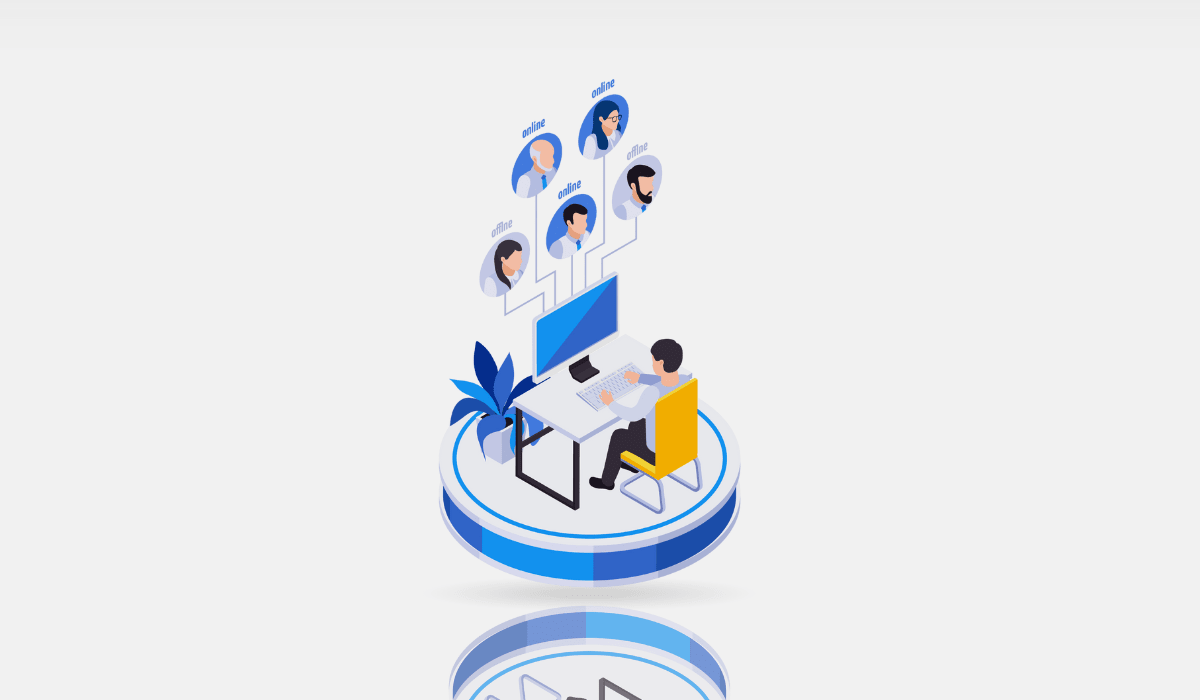
Effective inventory management is crucial for the success of any business operating in today’s dynamic and competitive market.
With the complexities of supply chains, fluctuating demand patterns, and ever-changing customer expectations, relying solely on manual inventory management methods is no longer sufficient.
In this digital era, businesses need robust solutions to streamline their inventory processes and maximize operational efficiency.
This is where inventory management software plays a pivotal role, offering a comprehensive set of tools and features to help businesses thrive in their inventory management endeavors.
In this guide, let’s discover the importance of choosing the right inventory management software for your business and explore key features, types of systems, common mistakes to avoid, and more.
Content Index
When it comes to managing your inventory, having the right software can make a world of difference.
Here are some key reasons why choosing the right inventory management software is crucial for your business:
Inventory management software helps businesses strike the right balance between overstocking and stockouts.
By leveraging historical data, demand forecasting algorithms, and real-time inventory tracking, the software ensures that businesses maintain optimal inventory levels.
This not only reduces carrying costs associated with excess inventory but also minimizes the risk of stockouts, thereby improving customer satisfaction.
Automation is a key feature of inventory management software that enhances operational efficiency.
Tasks such as order processing, inventory replenishment, and stock tracking are automated, reducing manual errors and saving time.
This allows employees to focus on strategic initiatives rather than mundane administrative tasks.
It leads to increased productivity and better utilization of resources.
One of the biggest challenges in inventory management is maintaining visibility across the supply chain.
Inventory management software provides real-time visibility into inventory levels, orders, shipments, and supplier information.
This transparency enables businesses to make informed decisions and identify bottlenecks.
It also helps them proactively address issues before they escalate, ultimately improving supply chain efficiency.
By centralizing inventory data and integrating it with other business systems such as accounting, sales, and procurement, inventory management software streamlines operations.
It facilitates seamless communication and collaboration across departments, eliminates silos, and fosters a more integrated approach to inventory management.
This end-to-end visibility and connectivity contribute to smoother workflows and faster order fulfillment cycles.
Inventory management software offers thorough and detailed reports and analytics, which provide useful information about inventory performance, trends, and costs.
Businesses can analyze data related to stock levels, turnover rates, supplier performance, and demand patterns to make data-driven decisions.
This actionable intelligence helps in identifying opportunities for optimization, reducing excess inventory, and improving overall inventory management strategies.
Efficient inventory management directly impacts customer service levels.
With inventory management software, businesses can fulfill orders accurately and promptly, reducing order processing times and delivery delays.
Additionally, features like real-time inventory tracking and order status updates empower customers with visibility into their orders, enhancing their overall experience and satisfaction.
Effective inventory management software ultimately leads to cost savings across various aspects of the business.
By optimizing inventory levels, reducing carrying costs, minimizing stockouts, and improving operational efficiency, businesses can lower overall inventory costs.
Moreover, better inventory management practices contribute to reduced waste, improved inventory turnover, and enhanced profitability.
Inventory management is a critical aspect of any business that deals with physical products, ensuring smooth operations.
From tracking stock levels to managing orders and analyzing data, robust inventory management software can streamline operations and improve efficiency.
However, with a myriad of options available in the market, choosing the right inventory management software for your business can be a daunting task.
Here are some important factors that you need to consider while choosing the inventory management software:
Start by identifying your specific inventory management requirements.
This could include features like batch tracking, multi-location support, barcode scanning, real-time updates, or integration capabilities with other systems such as accounting software or e-commerce platforms.
Understanding your needs will help narrow down the options and focus on solutions that align with your business goals.
Choose the right inventory management software that can scale alongside your business.
Consider factors like future growth projections, seasonal fluctuations in demand, and the ability of the software to handle increasing inventory volumes and complexities.
Scalability guarantees that your investment retains its worth even as your business grows.
Opt for user-friendly software with intuitive interfaces.
A system that is easy to navigate and understand will facilitate quicker adoption by your team members, reducing training time and potential errors.
Look for software that offers comprehensive training resources and ongoing support to ensure smooth implementation and usage.
Seamless integration with your existing systems is crucial for efficient operations.
Ensure that the inventory management software can integrate with other business tools such as accounting software, e-commerce platforms, point-of-sale (POS) systems, and customer relationship management (CRM) software.
Integration eliminates data silos, improves data accuracy, and enhances overall productivity.
Consider the total cost of ownership, including upfront costs, subscription fees, maintenance costs, and any additional charges for upgrades or support.
Evaluate the return on investment (ROI) based on the software’s features, benefits, and potential cost savings from improved inventory management and operational efficiency.
Balance cost considerations with the value and capabilities offered by the software.
Conduct thorough research and seek recommendations from industry peers or trusted sources.
Read reviews and testimonials from other users to understand their experiences with the software.
Pay attention to factors like performance, reliability, ease of implementation, customer support quality, and ongoing updates or improvements.
Learning from others’ experiences can provide valuable insights into the software’s suitability for your business.
When evaluating inventory management software, here are key features you should look for:
One of the core functionalities of inventory management software is inventory tracking.
This feature allows you to keep a real-time record of your stock levels, including product quantities, locations, and movements.
With accurate inventory tracking, you can avoid stockouts, overstocking, and discrepancies in your inventory data.
Look for software that offers barcode scanning, serial number tracking, batch tracking, and integration with IoT devices for automated tracking.
Efficient order management is essential for fulfilling customer orders on time and maintaining customer satisfaction.
A good inventory management software should handle all aspects of orders, such as processing, invoicing, shipping, and returns.
It should also support multiple sales channels such as e-commerce platforms, brick-and-mortar stores, and wholesale channels, ensuring seamless order processing across various channels.
Replenishment planning is crucial for maintaining optimal inventory levels and avoiding stockouts or excess inventory.
Look for software that offers intelligent replenishment planning features based on demand forecasting, lead times, safety stock levels, and reorder points.
Automated replenishment suggestions can help you make data-driven decisions and streamline the procurement process, saving time and reducing carrying costs.
Data-driven insights are essential for optimizing inventory management and making informed business decisions.
Choose software that provides robust reporting and analytics capabilities, including customizable reports, dashboards, KPI tracking, trend analysis, and inventory performance metrics.
Advanced analytics features such as ABC analysis, inventory turnover ratio, and dead stock identification can help you identify opportunities for improvement and cost savings.
Mobile accessibility is a must-have feature for inventory management software.
Ensure that the software offers mobile apps or a responsive web interface that allows you to manage inventory, track orders, and access key data from anywhere, anytime.
Mobile accessibility enables remote operations, real-time updates, and on-the-go decision-making, enhancing productivity and flexibility.
Various inventory management systems have emerged to address different needs and challenges.
Now let’s understand five key types of inventory management systems and understand how each one works.
The perpetual inventory system is a method where inventory levels are continuously updated in real time as goods are bought, sold, or used.
It relies on technology such as barcoding, RFID (Radio Frequency Identification), or inventory management software to track inventory movements accurately.
Each time a product is sold or received, the system automatically adjusts the inventory levels and provides up-to-date information on stock availability.
Advantages of Perpetual Inventory System:
– Real-time tracking of inventory levels.
– Enables timely decision-making regarding stock replenishment and ordering.
– Minimizes the risk of stockouts or overstocking.
– Facilitates accurate financial reporting by reflecting the current value of inventory.
In contrast to the perpetual system, the periodic inventory system involves physically counting and reconciling inventory at specific intervals, such as monthly, quarterly, or annually.
During these inventory counts, all stock on hand is tallied, and adjustments are made to reflect any discrepancies between recorded and actual inventory levels.
This method is often used by small businesses or those with simpler inventory needs.
Advantages of Periodic Inventory System:
– Relatively straightforward and suitable for businesses with fewer inventory transactions.
– Lower initial setup and technology costs compared to perpetual systems.
– Provides a comprehensive view of inventory levels at specific points in time.
The Just-in-Time (JIT) inventory system focuses on minimizing inventory holding costs by synchronizing production with customer demand.
In this system, inventory is only acquired and used when needed for production or sale, eliminating excess stockpiling.
Suppliers deliver raw materials or finished goods just in time for manufacturing or customer orders, reducing storage costs and the risk of obsolescence.
Advantages of Just-in-Time (JIT) Inventory System:
– Reduces carrying costs associated with excess inventory.
– Improves cash flow by reducing capital tied up in inventory.
– Promotes leaner and more efficient production processes.
– Enhances responsiveness to changing market demands.
The ABC inventory classification system categorizes inventory items based on their value and importance to the business.
Items are typically classified into three categories:
By classifying inventory items in this manner, businesses can prioritize their inventory management efforts, focusing on strategic inventory control measures for high-value items while adopting more relaxed policies for lower-value items.
Advantages of ABC Inventory Classification System:
The Vendor Managed Inventory (VMI) system is a collaborative approach where suppliers manage their customers’ inventory levels directly.
The supplier monitors the customer’s inventory data, such as stock levels and usage patterns, and takes responsibility for replenishing stock as needed.
This system shifts inventory management tasks, such as forecasting and ordering, to the supplier, streamlining the supply chain and reducing inventory holding costs for the customer.
Advantages of Vendor Managed Inventory (VMI) System:
To ensure a successful implementation, avoid these common mistakes when choosing the right inventory management software:
One of the most common mistakes businesses make when implementing inventory management software is failing to provide adequate training to their employees.
Without proper training, employees may not fully understand how to use the software effectively, leading to inefficiencies and errors in inventory management processes.
To avoid this mistake, invest in comprehensive training programs for all employees who will be using the inventory management software.
This training should cover not only the basic functionalities of the software but also best practices for inventory management and data entry.
Providing ongoing support and refresher training sessions can also help ensure that employees are using the software correctly and efficiently.
Another common mistake is neglecting regular inventory checks and audits.
Without regular checks, businesses may not be aware of discrepancies or inaccuracies in their inventory data, leading to stockouts, overstocking, or lost revenue.
Implement a regular schedule for inventory checks and audits to ensure that your inventory data is accurate and up to date.
Use the inventory management software to generate reports and conduct physical counts to reconcile any discrepancies.
By staying on top of your inventory levels, you can make informed decisions about restocking, purchasing, and sales strategies.
Having too many storage facilities can also be a mistake when it comes to inventory management.
While it may seem beneficial to have multiple locations for storing inventory, managing and tracking inventory across multiple facilities can be challenging and increase the risk of errors.
Evaluate your storage needs and consider consolidating your inventory into fewer facilities if possible.
This can streamline inventory management processes, reduce overhead costs, and improve overall efficiency.
If you must maintain multiple storage locations, ensure that your inventory management software can effectively track and manage inventory across all locations.
Disorganized storage systems can lead to inefficiencies, misplaced inventory, and difficulty in locating items when needed.
Poor organization can also result in overstocking of certain items while others run out of stock, leading to imbalances and lost sales opportunities.
Take sufficient time to organize your storage system logically and efficiently.
Use labeling, shelving systems, and location codes to categorize and track inventory items.
Make sure that employees are trained to follow the organization system consistently to minimize errors and improve inventory visibility.
The physical location of warehouses and storage facilities can impact the efficiency of inventory management processes.
If warehouses are not situated near workstations or shipping areas, it can lead to delays in fulfilling orders, increased transportation costs, and logistical challenges.
Ideally, warehouses and storage facilities should be close to workstations, shipping docks, and transportation hubs.
This can streamline the movement of inventory, reduce travel time, and improve overall operational efficiency.
If relocation is not feasible, consider optimizing transportation routes and scheduling to minimize delays and costs.
Finally, failing to utilize the real-time reporting capabilities of inventory management software is a common mistake that businesses make.
Real-time reporting provides valuable insights into inventory levels, sales trends, and order fulfillment status, allowing businesses to make data-driven decisions and respond quickly to changing market conditions.
Make sure that your inventory management software offers robust real-time reporting features.
Monitor key metrics such as stock levels, turnover rates, and order fulfillment times regularly.
Utilize this data to identify opportunities for improvement, adjust inventory strategies, and optimize overall inventory management processes.
Choosing the right inventory management software is a critical decision that can significantly impact your business’s efficiency, profitability, and customer satisfaction.
By understanding your needs, evaluating key features, considering different system types, and avoiding common mistakes, you can select a software solution that optimally meets your requirements.
Invest time in research, testing, and training to maximize the benefits of your chosen inventory management software and drive success for your business.
Read more related articles about inventory management software: